在印刷当中,我们怎么做到选择同样的纸张,同样油墨的情况下,不考虑其它工艺问题,有的印刷品的光泽相差很多,那么如果不用印刷后的覆膜上光的话,提高印刷品光泽也有很多种方法:
In printing, how can we choose the same paper and ink without considering other technological problems? The gloss of some printed products is quite different. If we don't use the coated film after printing, there are many ways to improve the gloss of printed products
光泽,作为视觉信息的一种,能对人的心理状态,情绪等许多精神方面产生重要影响,所以人们对于颜色的研究很早就开始了,对于客户来说,一件印刷品上的某个商品是需要有光泽,除工艺做上去的光泽,那么光在印刷上是否能体现出来,我们也来了解一下。
Gloss, as a kind of visual information, can have an important impact on people's mental state, mood and many other spiritual aspects, so people's research on color has been started very early. For customers, a certain product on a printed matter needs to be glossy. In addition to the glossy process, whether the light can be reflected in the printing, we also want to know.
1、改进酸性润版液。
1. Improve acid fountain solution.
以铭酸、磷酸为主,酸性越强,对油墨连接料和颜料的分解力,腐蚀了越大,致使印迹膜面粗糙,降低了光泽。
The stronger the acid is, the more corrosive it is to the ink binder and pigment, resulting in the rougher surface of the imprinted film and lower gloss.
2、降低油墨乳化度。
2. Reduce ink emulsification.
胶印中的油墨乳化过度大都是操作中水大墨多造成的,印迹看上去墨层很厚,但油墨分子成水包油的状态,干燥后光泽性非常差,而且还会产生一系列其它故障。水大墨多是胶印中比较犯忌的做法。
The ink emulsification in offset printing is mostly caused by the large amount of water and ink in the operation. The ink layer looks very thick, but the ink molecules are in the state of oil in water. After drying, the gloss is very poor, and a series of other faults will occur. Water ink is more taboo in offset printing.
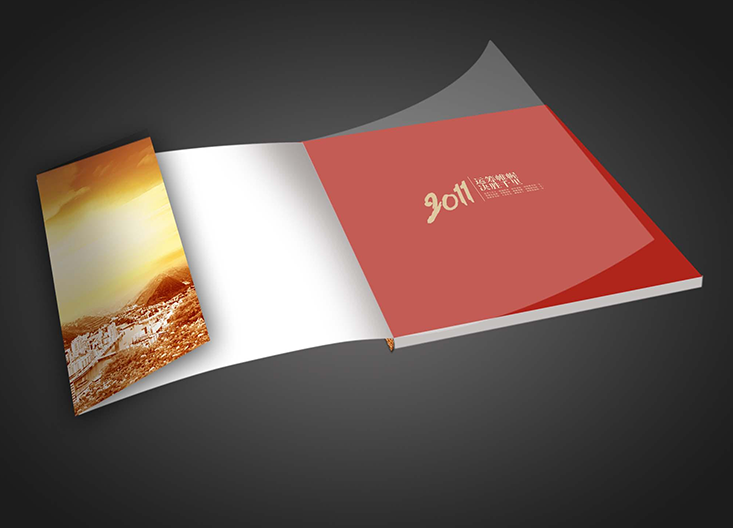
3、油墨中适当的加辅助剂。
3. Add appropriate auxiliary agent in the ink.
在油墨中适当的加辅助剂,可以调节油墨的印刷适性,以便顺利印刷,绝大部分辅助剂对于成品光泽都会带来不利影响,例如防粘剂,防粘剂主要原料为六谷粉,加入油墨后,印迹膜层表面由于玉米粉的析出而变的粗糙,成品光泽性就差。
The printing suitability of the ink can be adjusted by adding auxiliary agent properly in the ink, so as to print smoothly. Most auxiliary agents have adverse effects on the gloss of the finished product, such as anti adhesion agent. The main raw material of anti adhesion agent is Liugu powder. After adding the ink, the surface of the imprinted film becomes rough due to the precipitation of corn flour, and the gloss of the finished product is poor.
4.正确使用燥油。
4. Use dry oil correctly.
在工艺操作中,正确地使用燥油,对于成品形成光泽非常有利。这是因为纸张吸收连结料需要一定的时间,在此过程中,尽快使连结料凝聚,直结膜干燥,是成品光泽好的关键。
In the process operation, the correct use of dry oil is very beneficial for the finished product to form luster. This is because it takes a certain amount of time for the paper to absorb the binder. In this process, it is the key to make the binder condense as soon as possible until the conjunctiva is dry.
5. 注意喷粉。
5. Pay attention to dusting.
喷粉同油墨一样,也会产生凝聚,特别是密封不好的袋装或桶装,喷粉受潮后,凝聚成较大的颗粒,喷到湿墨印迹上,使墨层表面结膜粗糙,降低了原有的光泽,因此喷粉要注意防潮。
Dusting, like ink, will also produce condensation, especially in bags or barrels with poor sealing. When dusting is damped, it will condense into larger particles and spray on the wet ink mark, making the conjunctiva on the surface of the ink layer rough and reducing the original luster. Therefore, dusting should pay attention to moisture-proof.
6. 正确调节机器。印迹墨层厚度是否达到标准,对于光泽也有影响。例如压力调节不良,网点扩大率高,墨层厚度达不到标准,成品光泽就稍差。
6. Adjust the machine correctly. Whether the thickness of imprinted ink layer meets the standard also has an impact on the gloss. For example, poor pressure regulation, dot expansion rate, ink layer thickness does not meet the standard, the finished product gloss is slightly poor.
印刷压力也是印迹良好的转移关键,压力过大,印迹扩大,光泽度弱,压力过小,印迹不清晰,造成印品无光泽等,以上这些都是在印刷当中的一些细节方面需要注意的地方,正确的调节机器,印迹墨层厚度是否达标等,对于光泽也是有影响的。
Printing pressure is also the key to the transfer of good imprint. If the pressure is too large, the imprint will expand, the gloss will be weak, if the pressure is too small, the imprint will not be clear, resulting in the matte of the printed product, etc. These are some details that need to be paid attention to in the printing. Correct adjustment of the machine and whether the imprint ink layer thickness meets the standard also have an impact on the gloss.